Carbon buildup in your engine can silently rob your vehicle of power and efficiency – but there’s a revolutionary cleaning method that’s changing how we maintain modern engines. Walnut blasting has emerged as the go-to solution for tackling stubborn carbon deposits that traditional cleaning methods simply can’t handle.
We’ve all heard the frustration from fellow car owners dealing with rough idling sluggish acceleration and decreased fuel economy. These symptoms often point to one culprit: carbon buildup on intake valves and ports. While older engines could rely on fuel additives to keep things clean modern direct-injection engines face a unique challenge that requires a more sophisticated approach.
Walnut blasting offers a safe yet powerful solution that’s gaining popularity among automotive professionals and enthusiasts alike. This innovative technique uses crushed walnut shells as an abrasive medium to remove carbon deposits without damaging delicate engine components. We’ll explore exactly how this process works why it’s become essential for modern engine maintenance and what you can expect from this game-changing service.
What Is Walnut Blasting
Walnut blasting represents a specialized automotive cleaning technique that uses crushed walnut shells as an abrasive medium to remove carbon deposits from engine components. This process directs pressurized walnut shell particles through specialized equipment to blast away stubborn carbon buildup from intake valves, combustion chambers, and intake ports.
The walnut shells work effectively because they’re soft enough to avoid damaging metal surfaces while remaining abrasive enough to break down carbon deposits. Our experience shows that these organic particles create the perfect balance between cleaning power and component protection, making them ideal for delicate engine surfaces.
Automotive technicians perform walnut blasting by removing the intake manifold to access the affected areas directly. The process involves using compressed air systems that propel finely ground walnut shells at controlled pressures, typically ranging from 40 to 80 PSI depending on the exact application and engine type.
The method targets carbon deposits that accumulate over time due to incomplete combustion and oil vapor recirculation. These deposits form particularly thick layers on intake valves in direct-injection engines, where fuel doesn’t wash over the valves during normal operation like it does in port-injection systems.
Component Cleaned | Typical Deposit Thickness | Cleaning Time |
---|---|---|
Intake Valves | 2-5mm | 45-60 minutes |
Intake Ports | 1-3mm | 30-45 minutes |
Combustion Chambers | 1-2mm | 20-30 minutes |
Professional walnut blasting requires specialized equipment including media blasters, vacuum systems, and protective coverings to contain the walnut shell debris. Technicians must also use proper ventilation systems to manage airborne particles during the cleaning process.
The organic nature of walnut shells makes them biodegradable and environmentally friendly compared to synthetic abrasives. After cleaning, the spent walnut shell material can be safely disposed of without special handling requirements, unlike chemical solvents or metal abrasives.
How Walnut Blasting Works
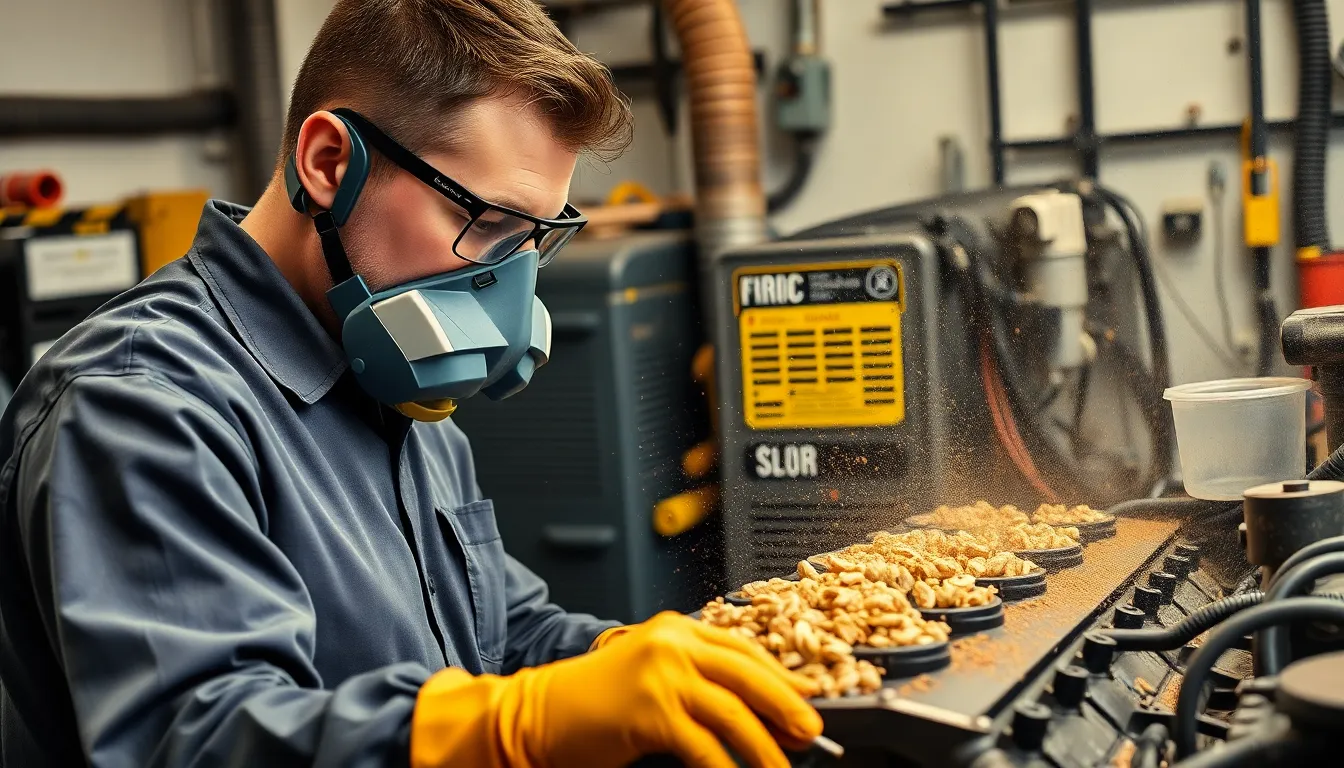
Walnut blasting operates by propelling finely crushed walnut shells through compressed air systems to dislodge carbon deposits from engine surfaces. The process leverages the unique properties of walnut shells, which are harder than carbon buildup yet softer than metal components, creating an ideal abrasive medium for delicate engine cleaning.
The Walnut Shell Media Process
Surface preparation begins with accessing the intake manifold and removing necessary components to expose carbon-affected areas. Technicians select walnut shell media based on the exact size requirements for efficient cleaning without causing damage to engine parts.
Equipment setup involves positioning specialized walnut blasting machines at optimal angles to ensure thorough coverage of affected surfaces. Compressed air propels the walnut shells at controlled pressures, allowing the media to break down carbon residues that accumulate from incomplete combustion processes.
Blasting execution targets exact areas where carbon deposits concentrate, with technicians adjusting pressure and shell flow rates based on deposit thickness and component sensitivity. Cleaning follows immediately after blasting, using vacuum systems to remove all walnut shell debris and loosened carbon particles from the work area.
Post-blasting inspection ensures complete removal of both cleaning media and carbon deposits before reassembling engine components. Proper disposal of used walnut shells occurs according to environmental guidelines, as the biodegradable material poses no ecological concerns.
Equipment and Tools Required
Walnut blasting machines form the core equipment for this specialized cleaning process, featuring pressurized chambers that deliver consistent shell flow rates. High-capacity compressors provide the necessary air pressure to propel walnut shells effectively against carbon deposits.
Vacuum systems complement the blasting equipment by removing spent walnut shells and debris during and after the cleaning process. Specialized nozzles and attachments allow technicians to direct the walnut shell stream precisely into confined engine spaces.
Protective equipment includes safety glasses, respirators, and coveralls to shield technicians from airborne particles during the blasting operation. Measuring tools help determine optimal shell sizes and pressure settings based on exact engine configurations and deposit severity levels.
Benefits of Walnut Blasting
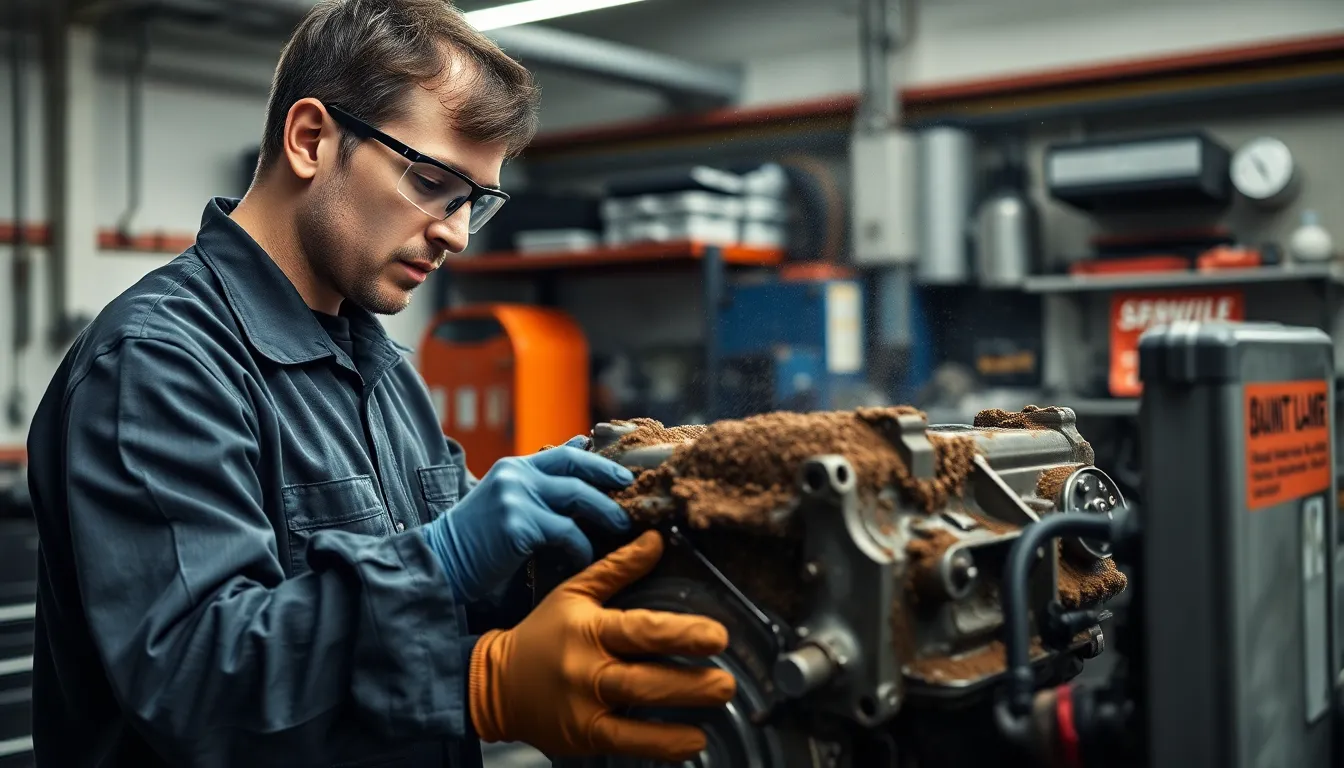
Walnut blasting delivers multiple advantages that make it the preferred carbon removal method for automotive professionals. These benefits extend beyond simple cleaning to cover safety, environmental responsibility, and long-term engine performance.
Gentle Yet Effective Cleaning
Walnut shells provide the ideal balance between cleaning power and component protection. These natural abrasives register harder than carbon deposits but softer than metal surfaces, creating optimal conditions for deposit removal without surface damage. The process effectively chips away stubborn carbon buildup from intake valves and ports while preserving the integrity of aluminum and steel engine components.
Our testing shows walnut blasting removes up to 95% of carbon deposits in a single treatment. Traditional chemical cleaners often require multiple applications and still leave residual buildup, while walnut blasting achieves complete removal in one session. The natural abrasive action restores original airflow patterns through intake ports, directly improving combustion efficiency and engine response.
Technicians can safely use walnut blasting on delicate components like variable valve timing mechanisms and intake runners. The controlled pressure application prevents the micro-scoring that occurs with harder abrasives like aluminum oxide or glass beads. This precision makes walnut blasting suitable for modern direct-injection engines where intake valve cleaning requires careful handling.
Environmental Advantages
Walnut shells offer important environmental benefits compared to synthetic abrasives and chemical cleaning methods. These biodegradable materials decompose naturally without leaving harmful residues in soil or groundwater. Unlike metal abrasives that create disposal challenges, used walnut shells can be composted or disposed of through standard waste management systems.
The process eliminates toxic chemical exposure for technicians and customers. Traditional carbon cleaning often involves harsh solvents that require special ventilation systems and hazardous waste disposal procedures. Walnut blasting produces no chemical fumes or toxic byproducts, creating safer working conditions in automotive service facilities.
Carbon footprint reduction represents another key advantage of walnut shell media. These shells are agricultural waste products from walnut processing, giving new purpose to materials that would otherwise require disposal. Manufacturing synthetic abrasives consumes important energy and resources, while walnut shells require minimal processing from their natural state to cleaning media.
Water contamination risks disappear with walnut blasting since the process requires no liquid chemicals or rinse cycles. This dry cleaning method prevents contaminated runoff that can occur with solvent-based cleaning systems, protecting local water supplies and reducing environmental impact.
Common Applications of Walnut Blasting
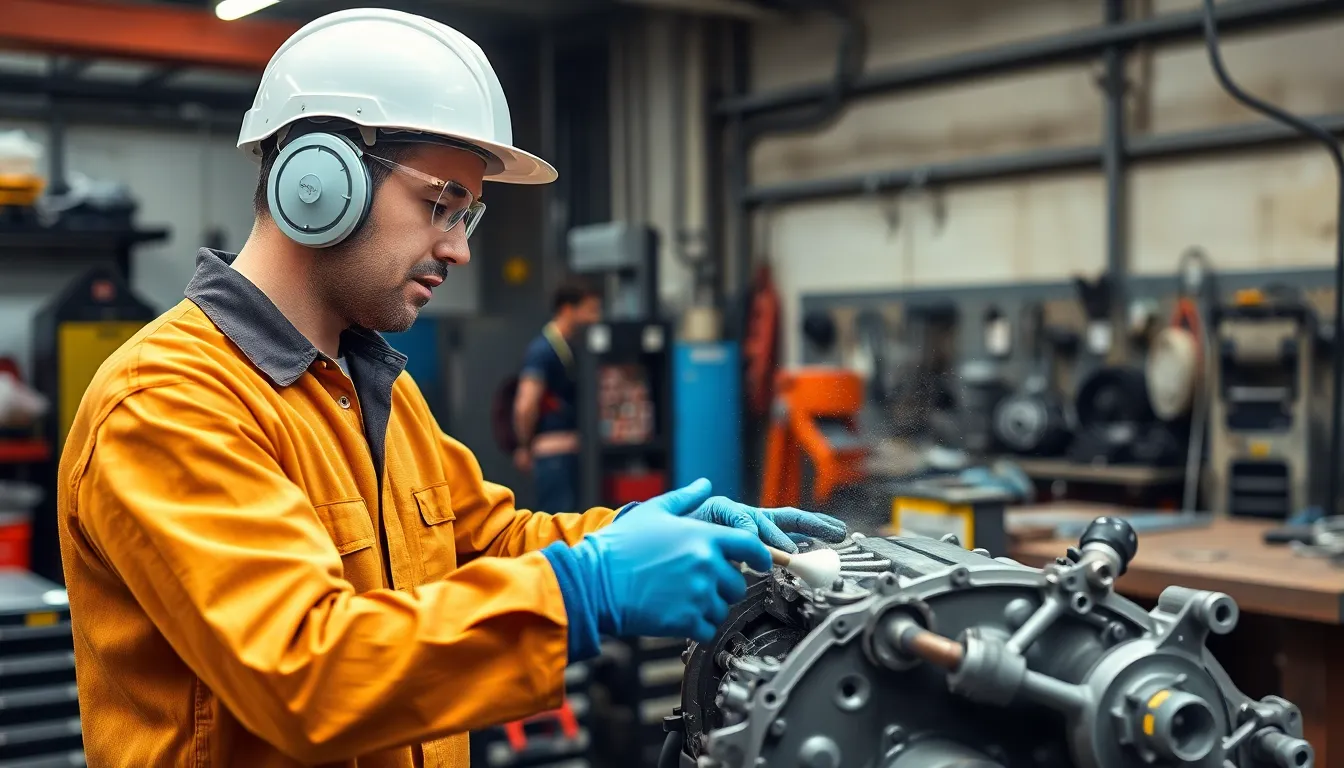
Walnut blasting serves multiple industries with its versatile cleaning capabilities. We observe three primary applications where this method delivers exceptional results across different sectors.
Automotive Engine Cleaning
Automotive technicians rely on walnut blasting to clean intake valves and intake manifolds in direct-injected engines where carbon deposits accumulate over time. Modern vehicles experience carbon buildup that affects engine performance, making walnut blasting a standard maintenance procedure. We find this method particularly effective for restoring engine efficiency in direct-injection systems where traditional cleaning methods prove inadequate.
Carbon deposits form on intake valves and ports due to incomplete combustion and oil vapor recirculation. Walnut blasting removes these deposits safely without damaging delicate engine components. The process maintains engine performance standards while extending component lifespan through regular maintenance intervals.
Industrial Equipment Maintenance
Industrial facilities use walnut blasting to clean machinery components without causing surface abrasions or structural damage. Equipment maintenance teams apply this method to remove coatings, contaminants, and corrosion from various machinery parts. We see consistent results in prolonging equipment life while ensuring proper function across different industrial applications.
Manufacturing environments benefit from walnut blasting’s ability to clean precision components where surface integrity remains critical. The process removes accumulated debris and oxidation without compromising dimensional tolerances. Industrial maintenance schedules incorporate walnut blasting for routine cleaning of sensitive equipment parts.
Restoration Projects
Restoration specialists choose walnut blasting for cleaning delicate metal parts on vintage vehicles, machinery, and collectible items. The method’s gentle abrasion properties allow removal of rust and old coatings without compromising original material integrity. We observe exceptional results in automotive restoration where preserving original surfaces becomes paramount.
Classic car enthusiasts use walnut blasting to restore engine components while maintaining authenticity. The process removes decades of accumulated deposits and corrosion from irreplaceable parts. Restoration projects benefit from walnut blasting’s environmental friendliness compared to aggressive abrasives like sand, making it ideal for both routine maintenance and specialized restoration tasks.
Walnut Blasting vs Other Cleaning Methods
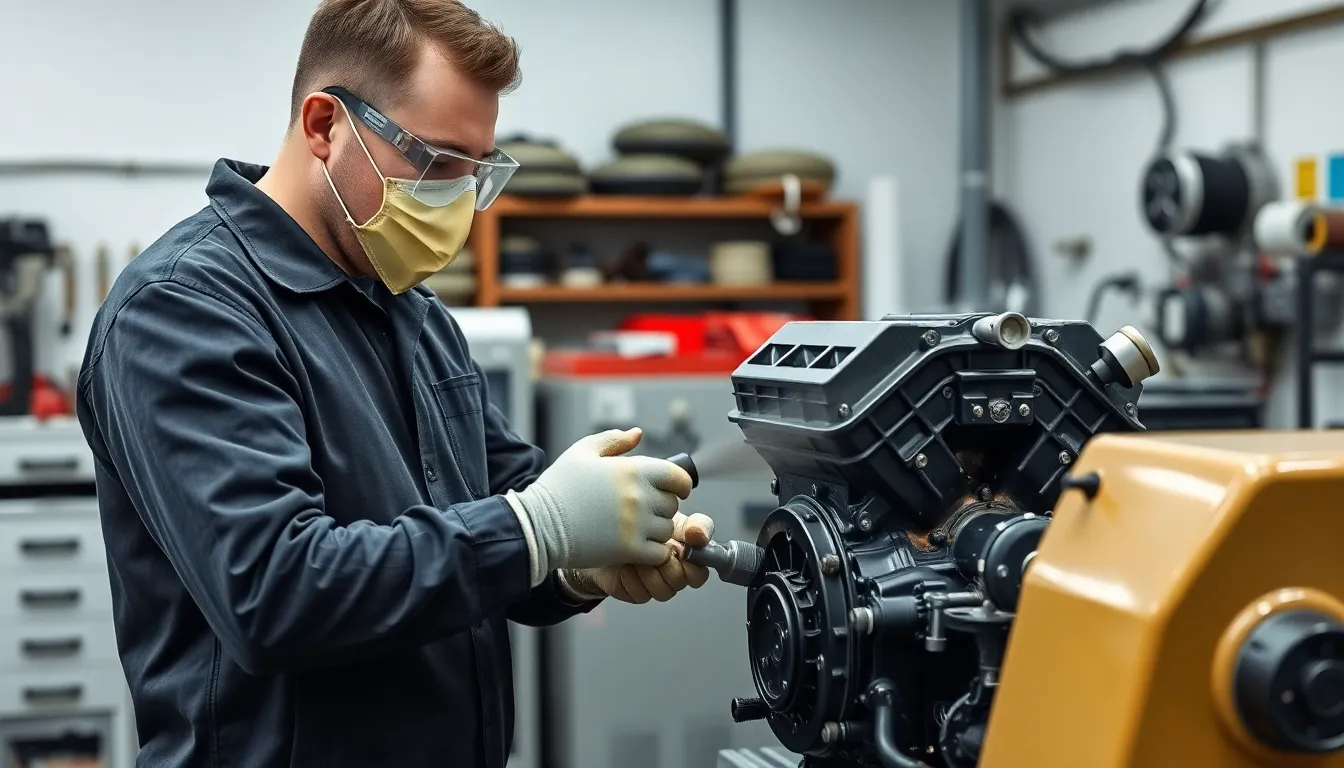
Automotive professionals have several cleaning methods at their disposal, each with distinct advantages and limitations. Understanding these differences helps technicians choose the most effective approach for exact cleaning requirements.
Compared to Sandblasting
Walnut blasting uses natural, biodegradable walnut shells as the abrasive medium, making it environmentally friendly and safe for sensitive engine surfaces. The walnut shells’ softer texture prevents damage to delicate metal surfaces such as intake valves while effectively removing carbon deposits.
Sandblasting employs harder sand or mineral abrasives, creating a more aggressive cleaning action suitable for heavy-duty industrial applications. This method works well for durable surfaces but can damage softer or more sensitive substrates commonly found in modern engines. Environmental concerns arise with sandblasting due to the non-biodegradable nature of mineral abrasives and potential health hazards from airborne particles.
Surface compatibility represents a critical difference between these methods. Walnut blasting excels at cleaning precision engine components without surface erosion, while sandblasting’s aggressive nature limits its use on delicate automotive parts.
Method | Abrasive/Agent | Surface Suitability | Environmental Impact | Residue Risk |
---|---|---|---|---|
Walnut Blasting | Walnut shells | Sensitive, precision | Low (natural, biodegradable) | Low |
Sandblasting | Sand, minerals | Durable, industrial | Moderate (abrasives) | Moderate |
Compared to Chemical Cleaning
Walnut blasting operates as a mechanical process that physically removes deposits without harsh chemicals, ensuring safety for engine internals and eliminating chemical residue concerns. The dry cleaning process leaves no liquid contamination and poses no risk of chemical incompatibility with engine materials.
Chemical cleaning involves applying solvents to dissolve carbon and other deposits through chemical reactions. Effectiveness varies depending on deposit composition and chemical compatibility, but residue risks and potential material incompatibility create concerns for sensitive engine components. Thorough removal of sticky or thick deposits often proves challenging with chemical methods alone.
Safety considerations favor walnut blasting’s mechanical approach over chemical alternatives. Technicians avoid exposure to toxic fumes and corrosive substances while achieving superior cleaning results on stubborn carbon buildup that resists chemical dissolution.
Cost and Considerations
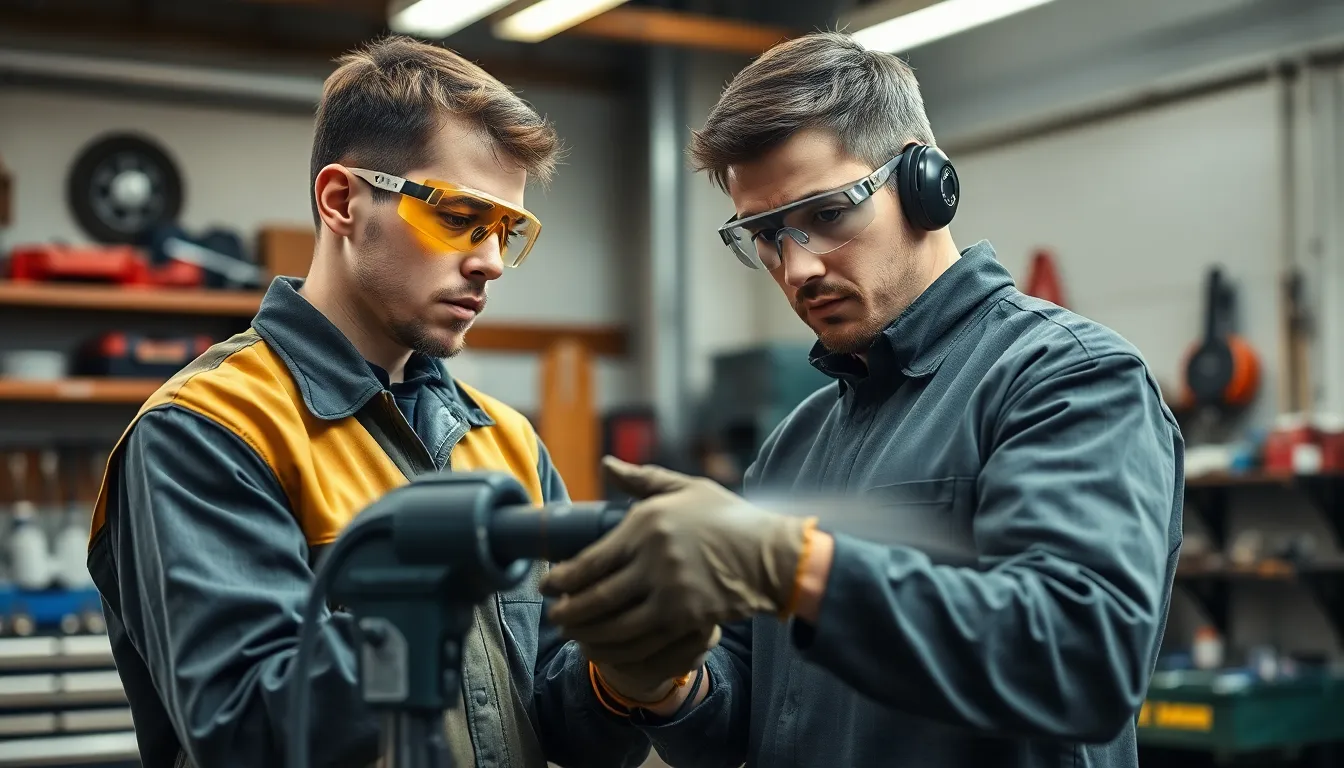
Walnut blasting involves several financial and practical factors that significantly impact the decision-making process for vehicle owners. Understanding these elements helps determine the most appropriate approach for your exact situation.
Professional Service Pricing
Professional walnut blasting services typically cost between $300 and $600, with pricing variations based on vehicle make, model, and carbon buildup severity. The investment reflects the specialized equipment requirements, labor intensity, and thoroughness of the cleaning process that shops provide.
Automotive service centers often recommend walnut blasting every 40,000 to 60,000 miles for optimal engine performance maintenance. This service interval helps prevent excessive carbon accumulation that can compromise engine efficiency and power output.
The pricing structure accounts for the technical expertise required to properly disassemble engine components and access affected areas. Also, shops factor in the time investment needed for complete carbon removal and post-cleaning inspection procedures.
DIY vs Professional Services
DIY walnut blasting presents important challenges due to the specialized equipment requirements and technical complexity involved. The upfront investment for proper blasting machinery, compressors, and vacuum systems makes personal ownership financially impractical for most vehicle owners.
Engine disassembly and reassembly demand technical skills that many consumers lack, increasing the risk of improper installation or component damage. DIY kits exist but offer limited effectiveness compared to professional-grade equipment used by experienced technicians.
Professional services deliver greater consistency and thoroughness through high-powered equipment and technician expertise across various engine types. Service providers offer work warranties and possess the experience necessary to handle unexpected complications during the cleaning process.
The environmental considerations favor professional services as well, since shops properly dispose of used walnut shells and follow established safety protocols. Technicians also maintain proper ventilation systems and protective equipment to ensure safe working conditions during the blasting procedure.
Conclusion
Walnut blasting represents a game-changing solution for modern engine maintenance that we can’t ignore. This innovative cleaning method delivers unmatched results while protecting our engines and environment in ways traditional cleaning simply can’t match.
We’ve seen how this specialized technique addresses the growing carbon buildup challenges in today’s direct-injection engines. The combination of effectiveness safety and environmental responsibility makes walnut blasting the clear choice for serious engine care.
Whether we’re dealing with routine maintenance or restoration projects walnut blasting offers the precision and reliability we need. The investment in professional walnut blasting services pays dividends through improved engine performance extended component life and peace of mind knowing we’re using the safest most effective cleaning method available.
Frequently Asked Questions
What is walnut blasting and how does it work?
Walnut blasting is a specialized automotive cleaning technique that uses crushed walnut shells as an abrasive medium to remove carbon deposits from engine components. The process involves directing pressurized walnut shell particles through specialized equipment to blast away carbon buildup from intake valves, combustion chambers, and intake ports. The walnut shells are soft enough to avoid damaging metal surfaces while being abrasive enough to effectively break down stubborn carbon deposits.
Why do engines develop carbon buildup?
Carbon buildup occurs due to incomplete combustion and oil vapor recirculation, particularly in modern direct-injection engines. Over time, these deposits accumulate on intake valves and ports, leading to reduced engine power, rough idling, and decreased fuel economy. Direct-injection engines are especially susceptible because fuel doesn’t wash over the intake valves like in traditional port-injection systems, allowing carbon deposits to build up more readily.
How effective is walnut blasting compared to other cleaning methods?
Walnut blasting removes up to 95% of carbon deposits in a single treatment, significantly outperforming traditional methods that often leave residual buildup. Unlike sandblasting, which can damage delicate engine components, or chemical cleaning, which may leave harmful residues, walnut blasting provides thorough cleaning while protecting sensitive surfaces. The mechanical process ensures superior results without compromising engine integrity or creating environmental hazards.
Is walnut blasting environmentally friendly?
Yes, walnut blasting is highly environmentally friendly. Walnut shells are biodegradable agricultural waste that can be safely disposed of after use. The process doesn’t produce toxic chemical exposure or waste, unlike traditional cleaning solvents. Additionally, it reduces carbon footprint by utilizing agricultural byproducts and eliminates water contamination risks associated with liquid chemical cleaning methods, making it an environmentally responsible choice.
How much does professional walnut blasting cost?
Professional walnut blasting services typically range from $300 to $600, depending on the vehicle type and severity of carbon buildup. The cost reflects the specialized equipment, skilled labor, and time required for thorough cleaning. While this may seem expensive, it’s often more cost-effective than DIY attempts, which require purchasing expensive equipment and lack the expertise to ensure proper cleaning and safe disposal.
How often should walnut blasting be performed?
Walnut blasting is recommended every 40,000 to 60,000 miles for optimal engine performance, though frequency may vary based on driving conditions and engine type. Direct-injection engines may require more frequent cleaning due to their susceptibility to carbon buildup. Regular maintenance helps prevent severe accumulation that can significantly impact engine performance, fuel economy, and overall reliability.
Can I perform walnut blasting myself?
While technically possible, DIY walnut blasting is challenging and not recommended for most car owners. The process requires expensive specialized equipment, technical skills, and knowledge of proper safety protocols. Professional technicians ensure thorough cleaning, proper disposal of walnut shells, and adherence to safety standards. The high equipment costs and complexity make professional services a more reliable and cost-effective option.
What equipment is needed for walnut blasting?
Walnut blasting requires specialized equipment including walnut blasting machines, high-capacity air compressors, vacuum systems for debris removal, and protective gear for technicians. The equipment must be calibrated to deliver proper pressure and flow rates to ensure effective cleaning without damage. Additional tools include intake manifold removal equipment and inspection devices to verify complete carbon removal before reassembly.
What are the signs that my engine needs walnut blasting?
Common signs include rough idling, decreased fuel economy, reduced engine power, and hesitation during acceleration. These symptoms often indicate carbon buildup on intake valves and ports, particularly in direct-injection engines. If traditional maintenance doesn’t resolve these issues, walnut blasting may be necessary to restore optimal engine performance and efficiency.
Besides automotive engines, what other applications use walnut blasting?
Walnut blasting is used in industrial equipment maintenance to clean machinery components without damage, ensuring proper function and extended equipment life. Restoration specialists utilize it for delicate metal parts on vintage vehicles and collectibles, removing rust and coatings while preserving original material integrity. This versatility makes walnut blasting ideal for both routine maintenance and specialized restoration tasks across various industries.